Hinckley, Leicestershire, United Kingdom, 21st Aug 2025 – Just Keepers Ltd has added a new goalkeeper glove to its collection, designed to perform in wet weather conditions. The release reflects ongoing efforts to provide goalkeepers with equipment that addresses performance challenges faced during adverse playing environments.
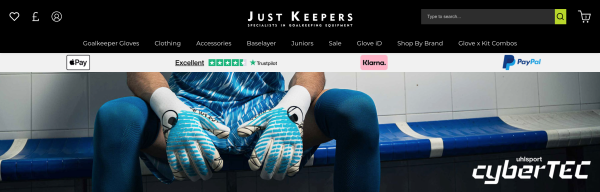
The newly added gloves incorporate aqua-focused technology that enhances grip and handling when surfaces are slippery. Through the use of these materials, the gloves aim to maintain consistent performance, even in heavy rain, ensuring that goalkeepers can rely on stability and control when it matters most.
A key consideration in their design has been player feedback, highlighting the need for gloves that remain dependable in challenging match situations. Just Keepers’ addition of wet weather gloves represents a practical response to those requirements, combining durability with specialist features for improved match confidence.
This addition further extends the company’s goalkeeper glove collection, offering solutions that consider the diverse conditions athletes face on the field.
Just Keepers Ltd continues to provide options for goalkeepers of all ages and abilities. The range extends from junior goalie gloves designed for young players taking their first steps in the game, through to professional-level equipment crafted for those competing at the highest standards.
More Information
https://www.just-keepers.com/goalkeeper-gloves/goalie-gloves/uhlsport-gk-gloves/
About Just Keepers Ltd
Just Keepers Ltd is dedicated exclusively to the art of goalkeeping. The company offers a wide selection of gloves, apparel, and specialist gear designed to meet the unique requirements of the position. Serving both aspiring players and experienced professionals, its collection is developed to support goalkeepers at every stage of their journey. With a strong emphasis on performance and reliability, Just Keepers has established itself as a trusted source for those who see goalkeeping as more than a position, but as a discipline in its own right.
Media Contact
Organization: Just Keepers Ltd
Contact Person: Just Keepers Ltd
Website: https://www.just-keepers.com/
Email: Send Email
City: Hinckley, Leicestershire
Country:United Kingdom
Release id:32739
The post Just Keepers Responds to Player Needs with Wet Weather Goalkeeper Gloves appeared first on King Newswire. This content is provided by a third-party source.. King Newswire makes no warranties or representations in connection with it. King Newswire is a press release distribution agency and does not endorse or verify the claims made in this release. If you have any complaints or copyright concerns related to this article, please contact the company listed in the ‘Media Contact’ section